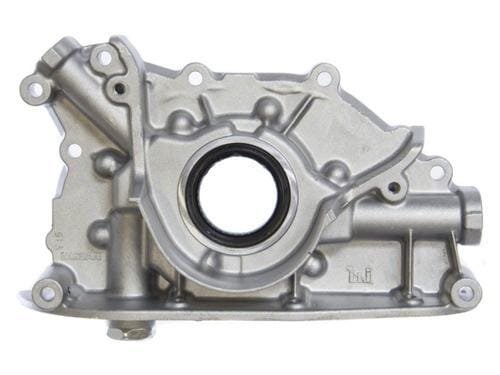
What need to know about low pressure casting
low pressure casting is a method of pressing liquid metal into a metal mold with pressure ranging from 8 to hundreds of ata.
Advantages:
+ High casting mechanics thanks to high casting density.
+ High productivity (100 ÷ 200 casting / hour) thanks to fast filling and favorable mechanization ability.
+ The casting has high precision and gloss (accuracy reaches 0.01 mm).
+ The inner surface of the casting is also highly glossy because the core of a metal cannot be used but the sand core cannot be used.
+ Casting thin objects (thickness> 0.3 mm) and complex objects (holes with a diameter of 1.5 ÷ 3 mm can be cast) because liquid metal is pressed into the mold, so it has good filling capacity.
+ Due to casting in a metal mold, the object cools quickly and has good mechanical properties.
Disadvantages of low pressure casting
+ Can not use sandblasting because the flow is pressurized. Hence the shape of the hole or the inside face must be simple.
+ Mold quickly wears out due to the pressure flow of the alloy at high temperature.
+ Less used for casting black metal because the melting temperature of black metal makes mold durability decrease.
Application
Application: Casting under pressure is used to manufacture complex details such as oil pump casing, pressure chamber cap, air valve, brass pipe, …
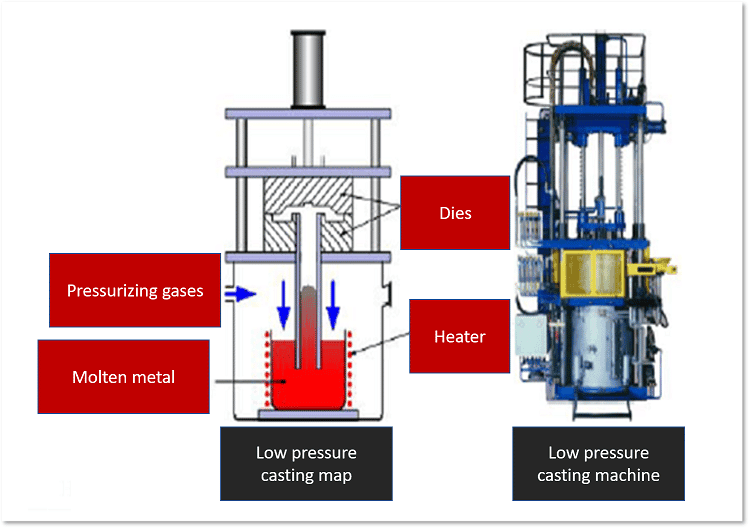
You might also want to know:
We Guarantee Successful Outsourcing
Best delivery performance, competitive pricing, better commercial terms, stable supplier base, control lead time
Effective and seamless workflow
With millions of parts delivered annually and serving more than 30 international customers, we are practicing the most advanced workflow to ensure the satisfaction of our customers and suppliers
-
7mil
-
98%
Free consultation
Book an online meeting within 24 hours