With 25 years of continuous research, innovation, and development, the mechanical processing industry, in particular, and the die casting industry in Vietnam, have made positive changes and used that as a lever to develop more and more. thrive. Up to now, mechanical processing has been one of the primary spearhead industries of the country, thereby creating the basis for promoting other industries such as agriculture, fishery, forestry, and service industries. services, as well as serving domestic needs.
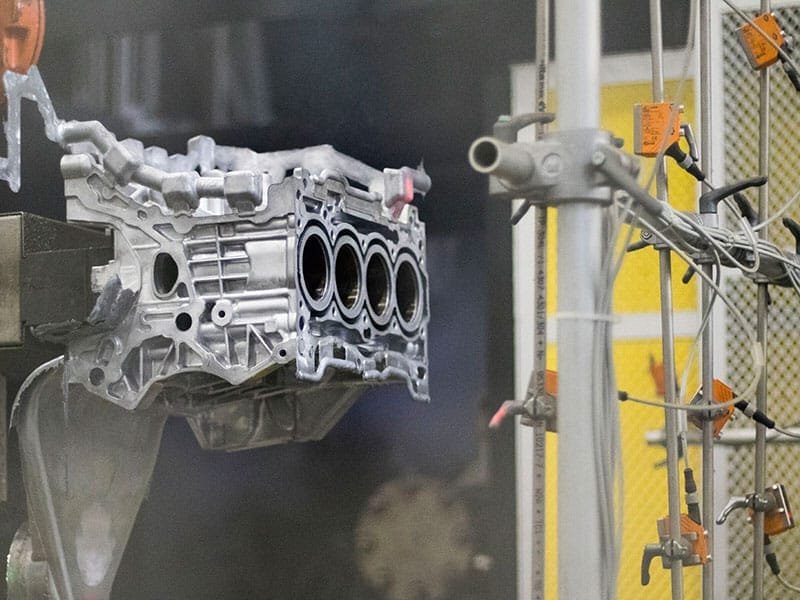
Positive signals from domestic sectors are also the first step to reaching foreign markets. With what the industry has shown in recent years, Vietnam’s mechanical processing industry is oriented to invest in developing the sector in businesses with good infrastructure and taking advantage of available strengths. The State will also have plans to gradually form supporting industries to maximize the general development needs of the mechanical industry.
In parallel, there are measures to modernize existing equipment, innovate in terms of technology, and apply digital technology in product design and manufacturing stages. With such investment, the mechanical processing industry is expected to reach the target of about 21% in the industry’s structure and meet about 50% of the demand of the domestic mechanical industry market. Up to now, enterprises are also focusing on improving the efficiency of operations management to increase the efficiency of investment, production, and business activities.
-
What is pressure casting technology?
Pressure casting is a method of manufacturing castings with very high productivity, which can operate on a fully automated mechanism, with high precision and surface gloss of castings. Currently, the output of castings made by the pressure casting method accounts for the most significant proportion of unique casting methods.
Today, the pressure casting process is carried out by specialized machines that are highly automated and mechanized. The simplicity and few steps in pressure casting open up great prospects for automating entire manufacturing processes.
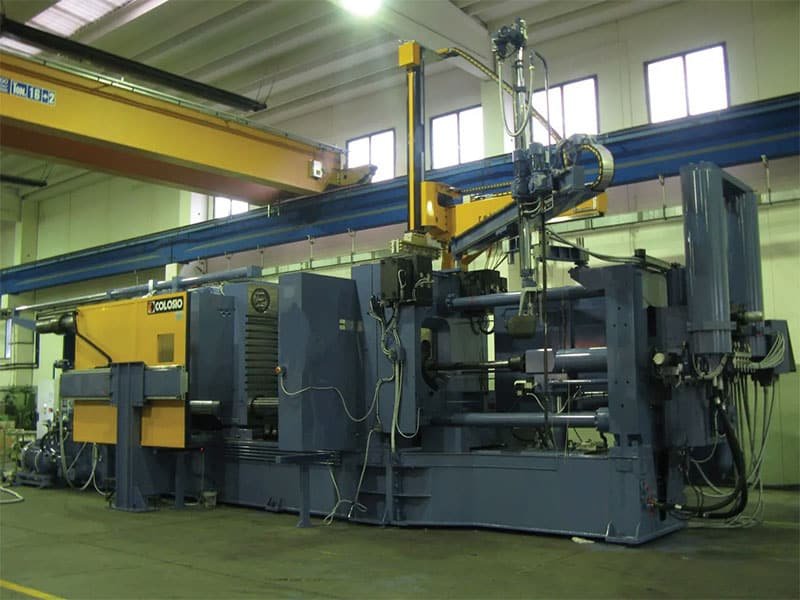
-
Advantages and disadvantages of die casting
2.1. Advantages
- Castings achieve precision and high surface gloss.
- Capable of casting very thin wall castings (<1 mm)
- Due to the considerable mold filling speed, high pressure acting on the liquid metal, and rapid cooling of the metal mold, the organization of the casting is small and tight.
- The high degree of mechanization and automation improved working conditions.
- High productivity.
- Metal molds can be used many times.
- Bringing different strengths, whereby in the diecast process, the product will have a much more robust feature than using plastic
- Making the production process faster, easy to perform injection molding with large volumes without too many cumbersome tools, takes little time to process products. Still, the efficiency and quality could be higher.
- The surface of product models made from diecast becomes smooth and smooth, with compatible curvature without worrying about corners, making it unsafe to use.
- The product sample is created with high accuracy. The application of advanced specifications helps the product create the right design, bringing satisfaction to customers when using.
2.2. Defect
- The cost of the mold is very high (the mold material must be a unique heat-resistant material, meticulously processed, and suitable for heat treatment).
- The casting machine’s size limits the casting’s size and mass.
- Only aluminum or copper alloys can be cast, not cast iron or steel.
- Besides the advantages, the die-casting process also has weaknesses that any compression molding engineer needs to understand to bring about high applicability and efficiency in his work:
- Die casting can reduce the budget and cause the model’s high performance to significantly reduce by increased volume.
- Sometimes the diecast process also limits the mobility of metals, and the product’s shape also changes after impact.
- The product samples from diecast are limited in quantity, size, and volume.
- The die-casting process can also present many product type variations, as die-casting produces only a single product. Therefore, many different molds must be created to serve the injection molding.
- In addition to the above information, die casting has countless other unique features that bring high performance if the mechanic knows how to use the die-casting process effectively.
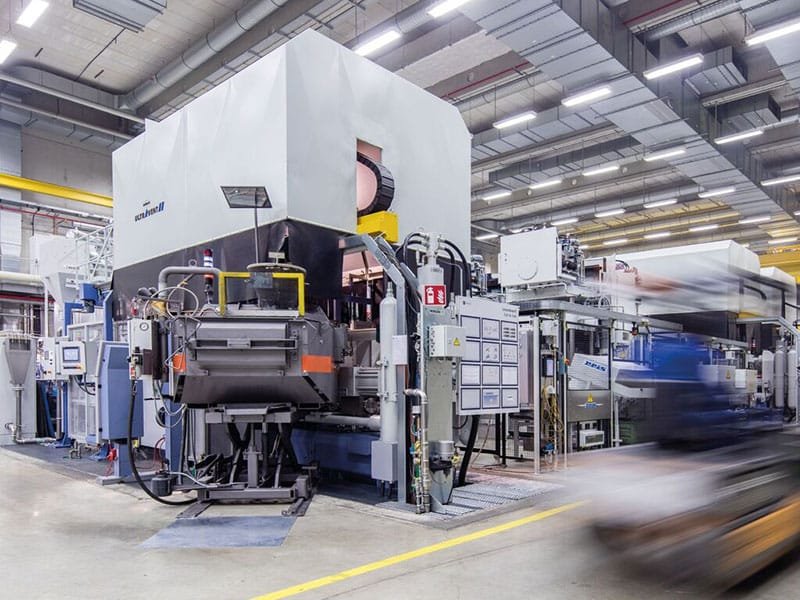
-
Metals commonly used in die casting
Some of the metals and composites used a lot in die casting include:
-
Aluminum
This is one of the most commonly used metals in the casting and pressing process today. However, when using aluminum in the die-casting process, the material is also prone to cracking or shrinking in size when cast at high temperatures.
Because of this feature, when casting pure aluminum, workers will combine it with other metals, such as copper or silicon. This will increase the tolerance of the product in the die-casting process.
-
Copper alloy
Copper alloy is also a continuous feedstock used in the casting process. Engineers and technicians use this material to deploy the diecast process to create applied mechanical products.
It is because copper and its synthetic metals have the advantage of resisting the corrosion of other acids. They are often used in the casting of water pipes as well as influential electrode conductors.
-
Zinc
Zinc is a metal that can be used quickly in casting and pressing. Exceptionally when, diecast is maintained and more durable at high temperatures.
Due to its low melting properties at high temperatures, service engineers rely on zinc to hot-cast the pole chamber efficiently. In addition, zinc will be used for production from the die-casting process compared to those that require high precision.
-
Magnesium
This lightweight alloy is advantageous compared to the die-casting process by providing high accuracy to the products.
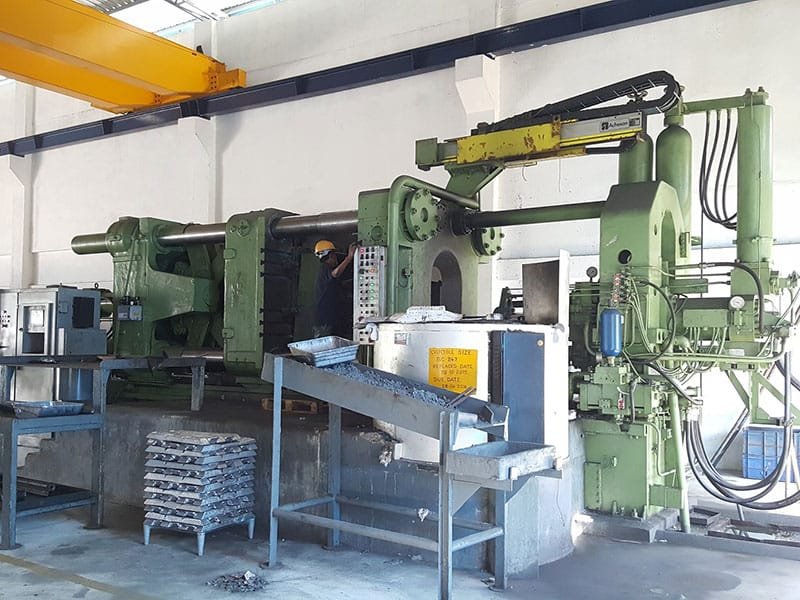
-
What are the precautions when using metal in the diecast process?
To select the suitable metal to use for the injection molding process, technicians must rely on the function of the diecast process and the products made to determine exactly.
For example, when selecting metals for diecasting, compared with products requiring high strength and adequate corrosion resistance.
Because of such requirements, engineers can thoroughly choose compatible materials such as copper or other alloys to conduct the most suitable product injection molding.
Furthermore, engineers need to communicate the volume of product types in production and which models have compatible maintenance characteristics. The materials used with long life and good durability should choose zinc, the operating cycle of this synthetic metal will be ten times higher than that of copper.
Currently, Vietnam is considered one of the reliable choices because of its responsiveness in terms of modern machinery, automation, and closed technology in processes from smelting raw materials to bringing raw materials to the market. into the mold until the final product is finished.
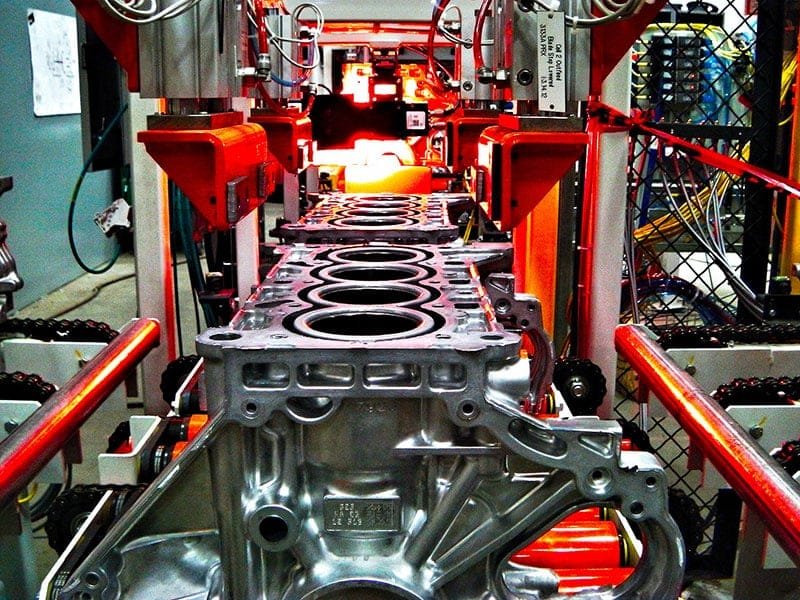
-
Die casting in Vietnam.
Die casting is one of the technologies that have contributed to Vietnam being named in the list of “reputable factories” worldwide. In recent years, high-pressure casting technology in Vietnam was gradually improving and affirmed a prominent role in production facilities. Pressure casting products are increasingly diverse, such as side covers, side arms…
Australia is one of the methods of product shaping. Based on material, product structure, technical requirements… People are divided into many different casting technologies, in which pressure casting is one of the most advanced and widely used casting methods.