- June 10, 2022
- Daniel Pham
How to cut down costs on your CNC projects
Understanding what factors lead to high costs, and identify a way to minimize or avoid them, is key to maximize efficiency and margins.
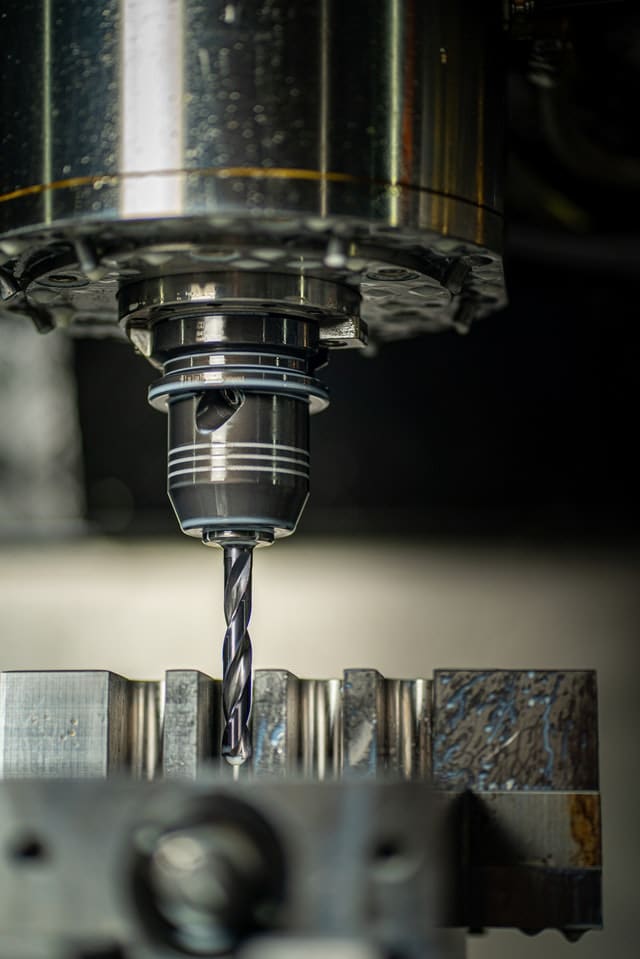
CNC milling is not a cheap process and you might be concerned about the costs spiraling out of control when you start a new project. In order to avoid the huge costs, the best way is to plan ahead and figure out which factor can be reduced or cut down to minize costs without compromising quality. Belows are a few tips for you to achieve cost-optimized projects.
1. Wise choice of raw materials
The cost of materials will be one of the biggest overheads in any project, so it pays to manage this with a particularly high level of care. For example, if you are just knocking up a prototype, there is no point splashing out on the best available materials when a lesser alternative will do just fine. Are you going to perform a short run of a particular component? Quality is of the essence in this case, so it might be smart to spend a bit more on the material.
2. Optimize setups to reduce downtime
Whenever you need to stop the machine and change the setup, this downtime will be costing you cash over the course of a project. Therefore it is far cleverer to keep the number of setups required to a minimum so that the machine can be up and running rather than lying dormant while alterations are made for the next step. Obviously the ideal in this scenario is that a single setup will be needed for a part to be completed, although aiming for fewer than six will be sensible for more complex projects.
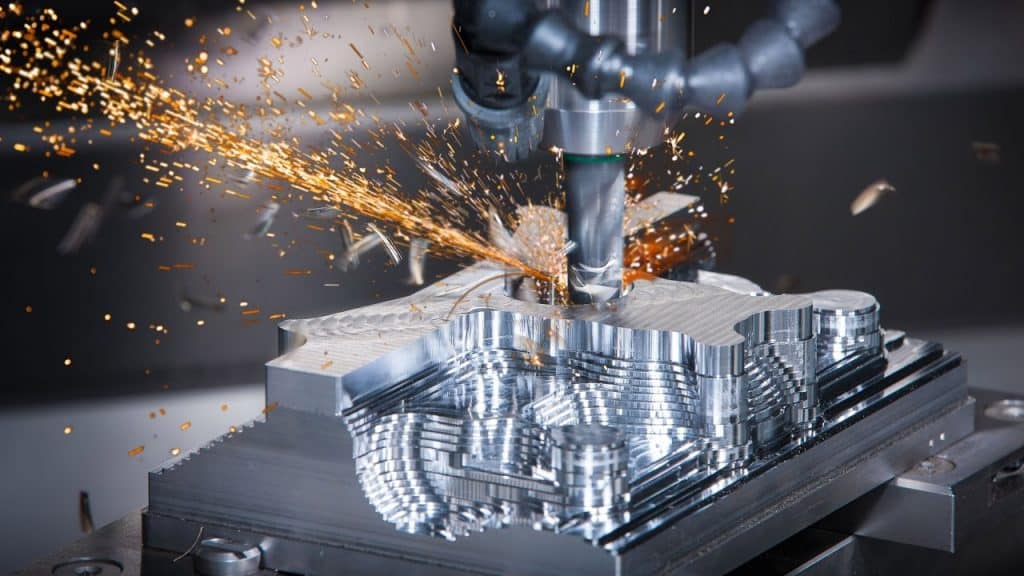
3. The loser the tolerances, the lower the costs
The more precision that is required to finish a component with a CNC milling machine, the greater the expenses involved, since if tight tolerances are not met, wastage will be inevitable. Conversely if you stick to standard tolerances that are easily achievable within the parameters of the equipment’s specifications, you will save time and therefore money.
Likewise it is sensible to use identical dimensions in the case that multiple holes need to be milled, both to reduce setup changes and to lower wear and tear on the tooling. If breakages occur, this will also result in downtime and additional outlay, which is obviously to be avoided. If it seems like your design is too complex, then it is better to go back to the drawing board sooner rather than later so that you are ready to push forward efficiently when the time comes to start prototyping.
4. Don’t sleep on NRE costs
There are a number of non-recurring engineering (NRE) costs that can crop up as part of any CNC milling project, especially if the aim is to eventually manufacture parts and products on a large, ongoing scale.
Because NREs are usually upfront expenses, if you can do your best to reduce them as soon as possible, then it will take less time for your project to become profitable once it is up and running.
Ultimately you need to see your CNC milling efforts as just one part of a wider process of turning a concept into a finished product. Because of this, your cost-cutting efforts should not just be focused on the machining process itself, but also on the other steps you need to take so that budgets are kept under control throughout.
Conclusion
Above listed a few key tips to help you on controlling the costs and thus, the profit of your CNC projects. However, these are just guidelines and abosolutely not written in rock. In the end, taking stock beforehand and planning ahead will always be key to achieve cost-optimized projects.